When it comes to a vehicle’s chassis and suspension system, most people first think of shock absorbers and struts. This might be due to car enthusiasts’ focus on modifying shock absorbers and the wide variety of options in the aftermarket. However, the prominence of these “star components” often overshadows other crucial chassis parts, such as ball joints and tie rods. Interestingly, many car owners and even mechanics sometimes confuse these two components, assuming they serve similar functions. In reality, they’re like a keyboard and a USB port—both essential parts of the vehicle system but with distinct roles, and neither can be spared (after all, without them, a vehicle can’t even steer properly).
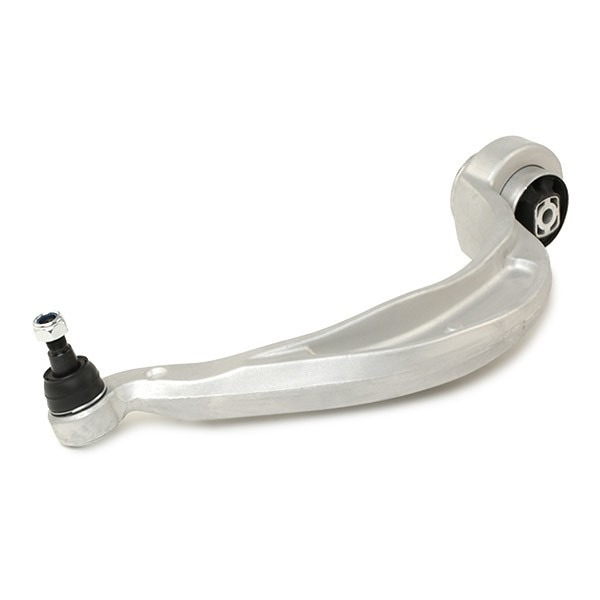
I. Why Do People Often Confuse Ball Joints and Tie Rods?
Modern passenger cars are equipped with both suspension and steering systems. The suspension system ensures a smooth ride on bumpy roads, while the steering system controls the vehicle’s direction. Components of these two systems are closely positioned in the chassis layout, making it easy to mix up ball joints and tie rods, which are key parts of each system. Moreover, misunderstandings about the term “ball joint” add to the confusion. The word “joint” suggests a flexible, rotating structure (like human joints), and ball joints do use a spherical design for 360-degree rotation and multi-directional movement. This intuitive impression blurs the line between their functions and those of rod-shaped parts like tie rods.
II. Fundamental Differences Between Ball Joints and Tie Rods
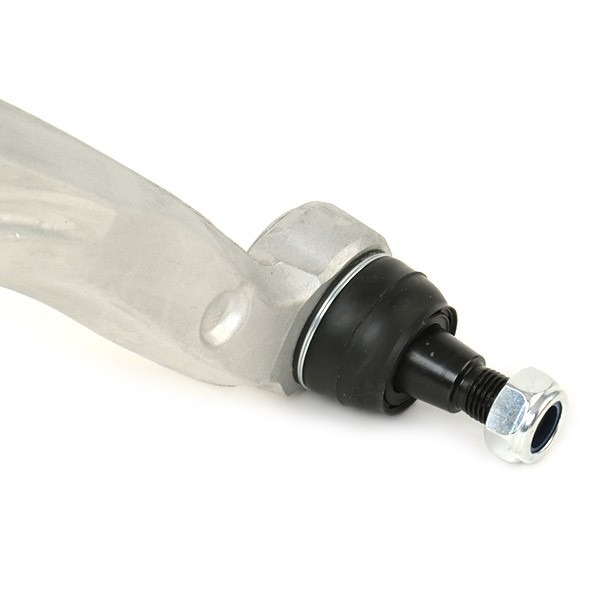
The core distinction lies in their belonging to different systems with entirely separate functional logics:
- Ball Joints:
These are mechanical connectors, primarily designed to enable flexible rotation and oscillation. Their name stems from the internal spherical structure, mimicking the movement of human joints. In automotive applications, ball joints are integral to three main components: sway bar links, control arms, and tie rods. Notably, when mechanics refer to “ball joints,” about 80% of the time they mean control arm ball joints—since these can often be replaced individually in most vehicle models (especially Japanese cars), while ball joints in sway bar links and tie rods usually require replacing the entire assembly. - Tie Rods:
Essential parts of the steering system, tie rods are roughly 20-inch-long rod-shaped components connecting the steering knuckle to the steering rack. When you turn the steering wheel, force transfers from the steering column to the steering gear, then to the tie rods, which move the steering knuckle and turn the wheels. Their lateral movement dictates the steering direction. To accommodate the wheels’ vertical movement due to road undulations, tie rods feature a specialized design that allows steering control without restricting wheel movement.
III. Structure and Components of Tie Rods
Tie rods consist of two main parts:
- Rack End:
One end connects to the steering rack, and the other end attaches to the tie rod end via external threads. The internal ball stud inside the rack end aligns parallel to the rack, enabling movement with the wheels without damaging the steering rack. This ball stud endures significant pressure during steering (e.g., when turning the wheel while stationary) and must maintain low torque for smooth operation. - Tie Rod End:
It contains a ball joint structure, linking to the wheel’s steering knuckle to turn the wheels. The other end connects to the rack end through internal threads, with a locking nut that adjusts the toe angle. Its design allows limited rotation and tilt (in most models, the tilt angle exceeds 50 degrees), and the ball joint usually faces downward to reduce water and debris intrusion.
IV. Applications of Ball Joints
In a vehicle’s chassis, ball joints mainly serve three components:
- Sway Bar Links: Connect the sway bar to the suspension system, reducing body roll;
- Control Arms: Link the vehicle frame to the wheels, transmitting road impacts and controlling wheel movement;
- Tie Rods: As mentioned, part of the steering system.
V. When Should You Replace Ball Joints and Tie Rods?
- Design Lifespan and Maintenance Tips:
Tie rods typically last over 60,000 miles. To extend their lifespan:
- Avoid turning the steering wheel while the vehicle is stationary (this subjects tie rods to tension equivalent to the weight of four adults);
- Slow down when driving over potholes to minimize impact loads.
- Identifying Fault Symptoms:
- Vehicle Pulling: If the car drifts while driving straight, it might indicate an unstable toe angle, requiring a tie rod check;
- Steering Wheel Misalignment: Sudden pulling of the steering wheel to one side after hitting a bump could signal a damaged tie rod ball joint;
- Unusual Noises or Vibrations: Intermittent knocking sounds or vibrations from the chassis may mimic control arm issues, but professional inspection is needed for accurate diagnosis.
VI. Conclusion
Ball joints and tie rods are like the “joints” and “nerves” of a vehicle’s chassis—the former adapt to complex road conditions with flexible movement, while the latter control steering precisely through lateral motion. Understanding their differences not only prevents misdiagnosis during repairs but also helps extend component lifespan through proper maintenance. When experiencing steering abnormalities or chassis noises, promptly checking these two components is key to ensuring driving safety.